The construction industry has seen remarkable technological advancements over the past few decades, from the adoption of Building Information Modeling (BIM) to the integration of drone surveys. Among these innovations, Real-Time Kinematic (RTK) technology stands out as a powerful tool that’s changing the way construction projects are planned and executed. While experienced contractors may be familiar with GPS technology, RTK takes it to a new level of precision and utility. This article will provide an in-depth explanation of RTK, how it works, and its diverse applications in the construction industry, particularly for those who are experienced in construction but new to RTK.
The Mechanics of RTK in Construction
Applications of RTK in Construction
Advantages of Using RTK in Construction
Challenges and Considerations When Implementing RTK
Understanding RTK Technology
What is RTK?
Real-Time Kinematic (RTK) technology is a specialized form of GPS that significantly enhances the accuracy of positioning data. Standard GPS systems, commonly used in smartphones and car navigation systems, offer accuracy within a few meters. While this might be sufficient for everyday use, such margins of error can be detrimental in construction, where precision is crucial. RTK improves this accuracy to within centimeters by using a fixed base station and one or more mobile units called rovers.
Originally developed for applications like land surveying, RTK has found a vital role in construction due to its ability to provide real-time corrections to positioning data. The base station, positioned at a known location, continuously compares its calculated position to its actual known position. The difference between these two values is the error, which the base station sends to the rovers. These rovers then adjust their GPS data accordingly, resulting in extremely precise positioning.
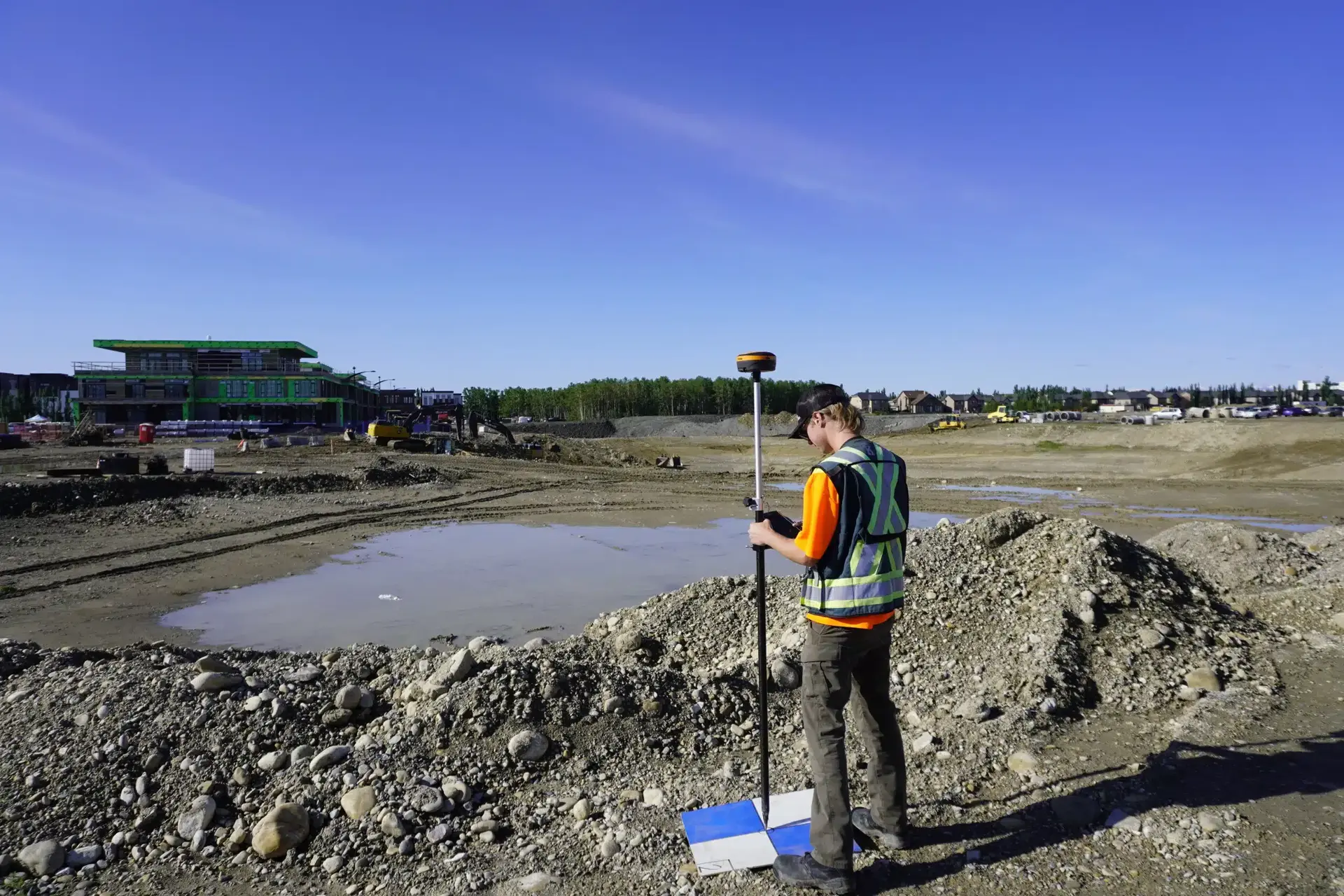
RTK being used for the establishment of ground control points for a site survey to be used in a topographic survey.
How Does RTK Work?
RTK operates by enhancing the GPS signals through real-time corrections. The system comprises two main components: the base station and the rover. The base station is set up at a known, fixed location and acts as a reference point. It continuously monitors the satellite signals and calculates the difference between its known position and the position calculated by the GPS signals. This difference, or correction, is then transmitted to the rover, which is a mobile unit operating in the field.
The rover receives these corrections via radio signals, internet, or cellular networks, depending on the system setup. With this corrected data, the rover can determine its position with centimeter-level accuracy, a significant improvement over the several meters of accuracy provided by standard GPS systems. This high level of precision is essential in construction, where even small errors can lead to significant issues in project execution.
The Mechanics of RTK in Construction
What Does an RTK Construction Setup Require?
In a construction context, RTK technology integrates seamlessly with various types of equipment and tools to enhance accuracy and efficiency. The primary components include:
Base Stations: These are typically portable units placed on-site at a known location. The base station must be set up in an area with a clear view of the sky to maintain strong satellite signals.
Rovers: These are mobile units that can be attached to machinery like excavators, graders, or used as a standalone receiver. The rover receives correction data from the base station and adjusts its GPS coordinates in real-time.
Antennas: These are used to receive satellite signals and can be mounted on construction machinery or survey poles. The antennas are then connected to hardware via cables.
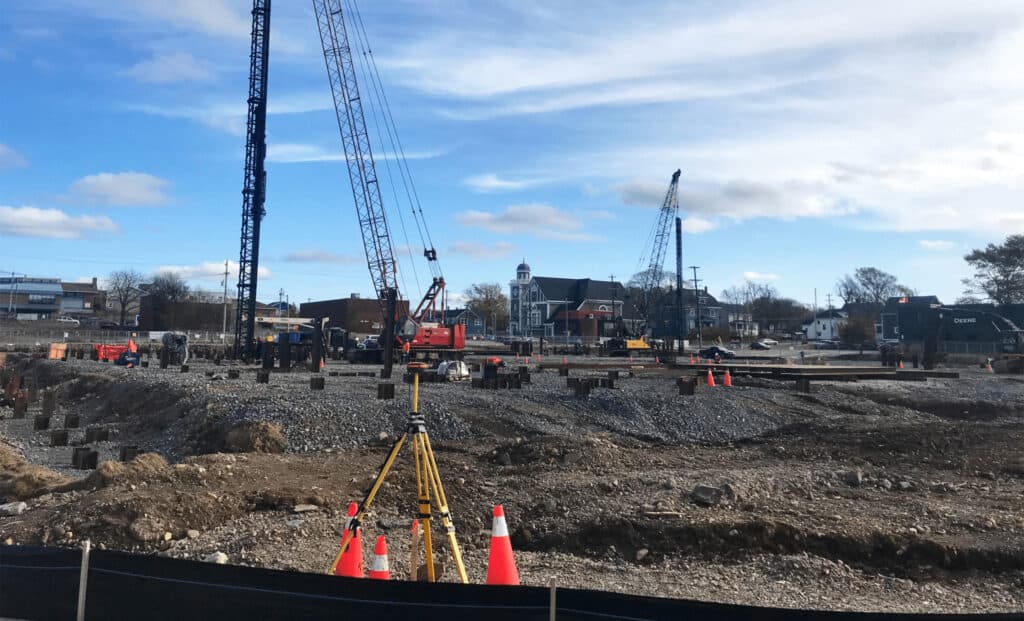
A typical base station setup on a construction site. The base station sits at a stationary location and provides the entire site with RTK corrections.
RTK Workflow on a Construction Site
Implementing RTK on a construction site begins with setting up the base station in a location that is central to the project area and has an unobstructed view of the sky. Once the base station is established, it starts receiving GPS signals and calculating the necessary corrections.
The rover, mounted on construction equipment or carried by a surveyor, receives these correction signals in real time. This allows the operator to perform tasks with a high degree of accuracy, such as grading, excavating, or laying out foundations. As the equipment moves around the site, the rover continuously updates its position relative to the base station, ensuring that every movement is precise. Systems like the Hemisphere S631 and Trimble’s R10 are examples of base and rover systems commonly used around construction sites.
For example, when grading a site, the machine operator can follow the digital design loaded into the machine’s control system, with the RTK system providing continuous, real-time updates on the machine’s exact position. This ensures that the grading is done according to the plan, with minimal errors and rework.
Benefits Over Traditional Methods
Traditional construction methods rely heavily on manual surveying and staking, which are time-consuming and prone to errors. In contrast, RTK provides several advantages:
Increased Accuracy: RTK delivers centimeter-level precision, with a significantly easier learning and operating curve when compared to older equipment like total stations and theodolites.
Time Efficiency: With real-time data correction, tasks such as grading and excavating are completed faster, reducing project timelines. RTK is capable of being used by a single operator, and does not require a crew with an instrument man and rod man.
Cost Savings: Fewer errors mean less rework, which translates to lower labor costs and material wastage. With RTK even relatively new users can use the equipment, meaning you don’t need to have an experienced operator. With our Survey-Assistant.com training academy, even a completely new user can get started.
Improved Workflow: RTK allows for seamless integration with digital construction plans, enhancing overall workflow efficiency.
Applications of RTK in Construction
Site Surveying
One of the most common uses of RTK in construction is for site surveying. Accurate site surveys are critical at the beginning of any construction project to define the boundaries, identify potential obstacles, and plan the layout of structures. RTK technology enables surveyors to conduct these tasks with high precision, reducing the likelihood of errors that could delay the project.
For instance, during a site survey, RTK can be used to establish the exact locations of boundary lines, utilities, and other critical features. This information is crucial for ensuring that the construction plan aligns perfectly with the actual site conditions.
We have several customers who use RTK to perform preliminary site surveys for construction layout. This includes identifying property lines, marking utilities, locating hazards and performing initial topographic work.
Machine Control
RTK technology is a game-changer in the realm of machine control, particularly for tasks like grading, excavating, and paving. Machine control systems equipped with RTK allow operators to achieve precise movements of their machinery, guided by digital design files loaded into the machine’s control system.
For example, in automated grading, the RTK system ensures that the grader follows the exact contours specified in the design, resulting in a perfectly leveled surface with minimal need for manual adjustments. Similarly, in excavation, RTK enables the operator to dig to the exact depth required, ensuring that the foundation is level and consistent across the entire site.
This level of precision not only improves the quality of work but also reduces the time spent on these tasks, as operators can rely on the RTK system to guide them accurately without needing to constantly check and recheck measurements manually.
One of our local customers uses RTK extensively in the preparation of grade for their machines. This includes performing topographic surveys to generate 3D maps for their operators, as well as tying in RTK for their drones and heavy machinery.
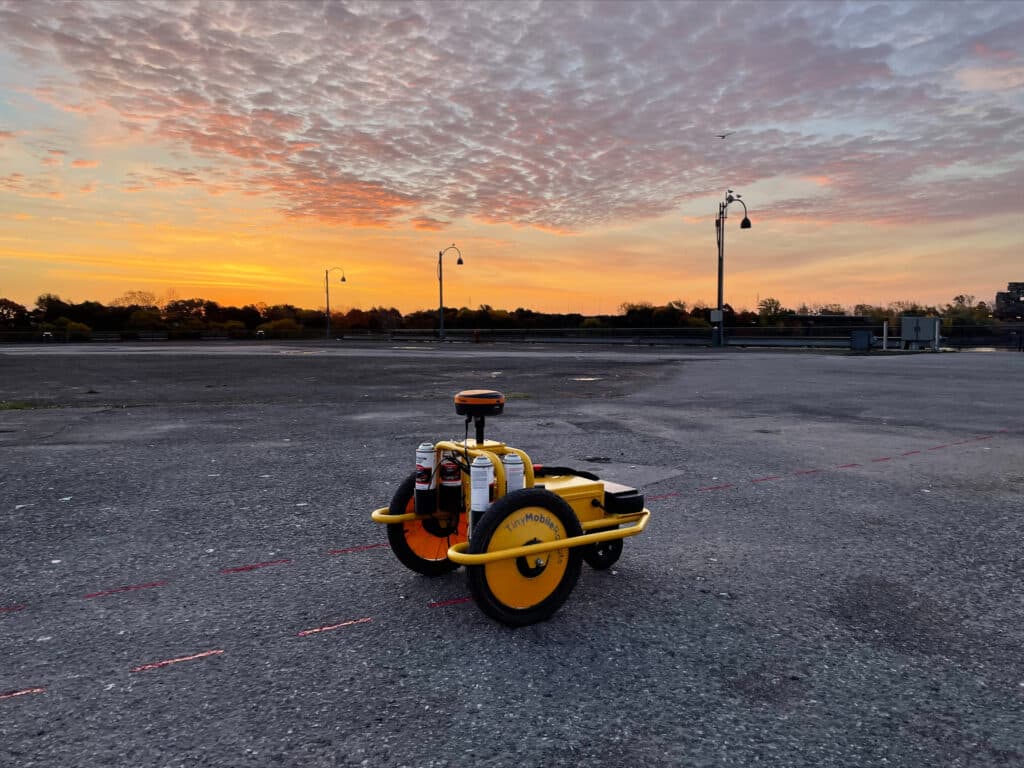
Machine control is not only for large heavy equipment. It is being used more and more for applications where autonomous control and high precision are required. This Tiny Mobile Robot was used to layout markings for a circus tent.
Foundation and Structural Layout
Laying foundations and structural components accurately is crucial to the integrity of any construction project. RTK ensures that the placement of these elements aligns perfectly with the architectural and engineering plans.
For example, when laying the foundation for a high-rise building, even a small deviation from the planned layout can have significant consequences. RTK allows contractors to position foundation corners and other critical points with precision, ensuring that the structure is built on a solid and correctly positioned base.
In structural layouts, RTK can be used to position columns, walls, and other elements accurately, minimizing the risk of misalignment that could compromise the building’s stability.
Utilities and Infrastructure
Mapping and installing utilities like water, gas, and electricity require precise measurements to avoid conflicts with other infrastructure and ensure efficient service delivery. RTK is invaluable in this process, providing the accuracy needed to map existing utilities and guide the installation of new ones.
For example, when installing underground utilities, RTK can help ensure that pipes and cables are laid in the correct locations, at the correct depths, and with the proper slope. This prevents issues like pipe clashes, leaks, and inefficient drainage, which can be costly and difficult to fix after the fact.
Additionally, RTK can be used to map existing utilities, creating accurate records that can be referenced in future projects. This is particularly useful in urban environments, where space is limited, and avoiding existing infrastructure is critical.
As-Built Surveys
As-built surveys are conducted to document the exact location and dimensions of structures after they have been constructed. These surveys are essential for ensuring that the project has been completed according to the design specifications and for creating accurate records for future maintenance or modifications.
RTK enhances the accuracy of as-built surveys, allowing surveyors to capture precise data on the location of structures, utilities, and other features. This data can then be compared with the original design plans to identify any deviations and ensure that the project meets all specifications.
For example, after completing the construction of a road, an as-built survey using RTK can document the exact location, elevation, and alignment of the road, providing valuable information for future maintenance and upgrades.
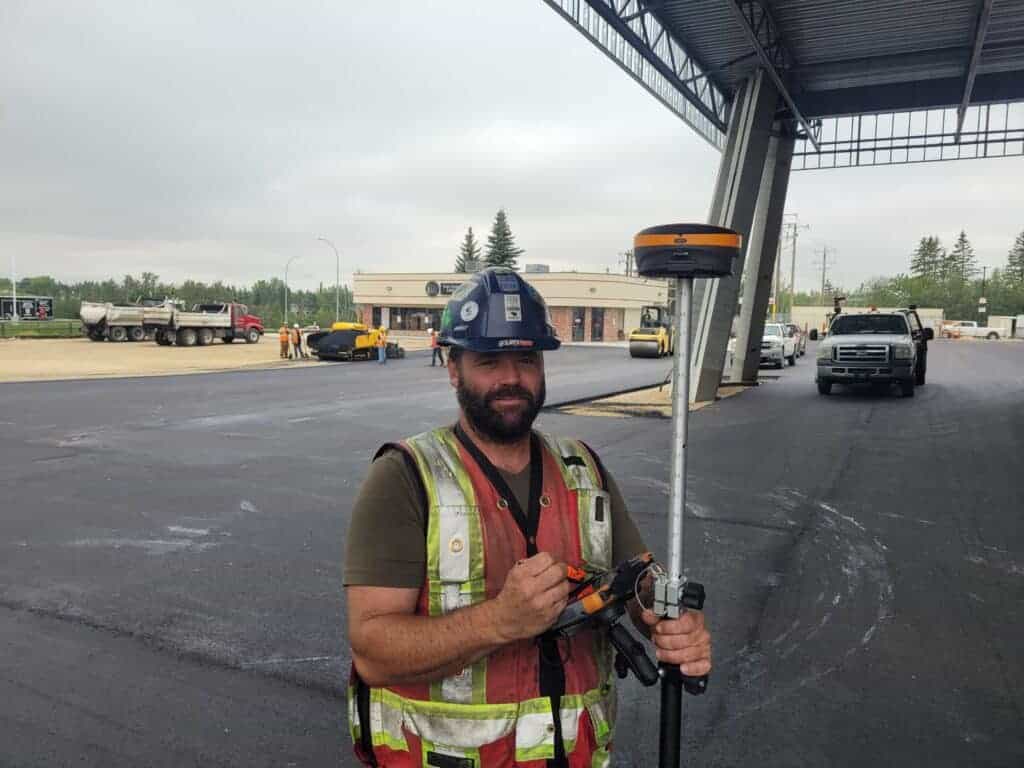
RTK is perfect for recording as-built surveys. Unlike total stations which require line of sight to make a measurement, RTK can record measurements anywhere.
Advantages of Using RTK in Construction
Precision and Accuracy
The most significant advantage of RTK in construction is its precision. By providing centimeter-level accuracy, RTK ensures that construction tasks are performed with the highest level of precision, reducing the risk of errors and rework.
This precision is particularly important in projects where even small deviations can have significant consequences, such as in the construction of high-rise buildings, bridges, and other critical infrastructure.
Time and Cost Efficiency
RTK significantly reduces the time required for tasks like surveying, grading, and excavation. By automating these processes and providing real-time corrections, RTK enables contractors to complete projects faster and with fewer errors. This not only shortens project timelines but also reduces labor costs and material wastage, leading to significant cost savings.
Safety Improvements
By reducing the need for manual measurements and adjustments, RTK minimizes the risk of human error, which can lead to accidents and safety hazards on construction sites. Additionally, RTK can be used to create more accurate safety plans, such as ensuring that temporary structures like scaffolding are placed correctly and securely.
Challenges and Considerations When Implementing RTK
Initial Setup Costs
While RTK offers significant benefits, the initial cost of purchasing and setting up an RTK system can be a barrier for some contractors. However, the return on investment (ROI) can be substantial, with savings in time, labor, and materials often offsetting the initial expenses.
Signal Reliability
RTK relies on strong, uninterrupted signals from GPS satellites, as well as reliable communication between the base station and the rover. In environments with poor satellite visibility, such as dense urban areas or sites with heavy tree cover, signal reliability can be a challenge. Contractors should be aware of these limitations and plan accordingly.
Final Thoughts
RTK technology is revolutionizing the construction industry by providing the precision and accuracy needed for modern projects. For experienced contractors unfamiliar with RTK, adopting this technology can lead to significant improvements in efficiency, cost savings, and project quality. As the industry continues to evolve, RTK is likely to become an essential tool for contractors looking to stay competitive and deliver high-quality results.
FAQs
What is RTK and how does it differ from standard GPS?
RTK (Real-Time Kinematic) is a technology that enhances the accuracy of GPS positioning from meters to centimeters. While standard GPS is accurate within a few meters, RTK achieves much higher precision by using a fixed base station and one or more mobile rovers that receive real-time correction signals. This allows for centimeter-level accuracy, which is crucial for precise construction tasks.
What are the primary components required for an RTK setup on a construction site?
An RTK system typically requires the following components:
Base Station: A stationary unit set up at a known location that calculates and transmits correction data.
Rover: A mobile unit attached to machinery or carried by surveyors that receives correction data from the base station.
These components work together to provide real-time, high-precision positioning on the construction site.
How is RTK technology applied in construction projects?
RTK is used in several key areas of construction:
Site Surveying: For precise boundary marking and site measurements.
Machine Control: To guide construction equipment like graders and excavators for precision tasks such as grading and excavating.
Foundation Layout: Ensures accurate placement of foundations and structural components.
Utilities and Infrastructure: Helps in mapping and installing underground utilities with high precision.
As-Built Surveys: Used to document the exact location and dimensions of completed structures.
What are the advantages of using RTK in construction compared to traditional methods?
Precision: Centimeter-level accuracy reduces errors and rework.
Time Efficiency: Real-time corrections speed up tasks like grading and excavation, reducing overall project timelines.
Cost Savings: Fewer errors lead to lower labor costs and material waste.
Safety: Minimizes human error and enhances on-site safety by providing accurate data for critical decisions.
What challenges should contractors consider when implementing RTK technology?
Some challenges of adopting RTK technology include:
Initial Setup Costs: The cost of RTK equipment can be high, but the return on investment is significant due to savings in time and resources.
Technical Expertise: Proper training is necessary to effectively use RTK systems.
Signal Reliability: RTK relies on strong, consistent satellite signals, which can be problematic in areas with poor visibility or interference. Planning and site assessment are essential to mitigate these issues.
Bench Mark Equipment & Supplies is your team to trust with all your surveying equipment. We have been providing high-quality surveying equipment to land surveyors, engineers, construction, airborne and resource professionals since 2002. This helps establish ourselves as the go-to team in Calgary, Canada, and the USA. Plus, we provide a wide selection of equipment, including global navigation satellite systems, RTK GPS equipment, GNSS receivers, and more. We strive to provide the highest level of customer care and service for everyone. To speak to one of our team today, call us at 403-286-0333 or email us at [email protected].